MANTA has not sold on eBay
A “MantaB” are not production quality MANTA
A 2014 batch of parts were found unsuitable for purpose, due to brittleness, the batch was rejected, brittle is the last thing you expect from this material, especially this grade
To illustrate the difference between production quality, and the “MantaB” we posted a 2014 video of the material comparison.
since then MANTA continued to develop, evolve
There have been structural changes since 2013
MANTA set quality control (QC) standards for parts along with DuPont, our toolmaker, our original manufacturing partner’s, Protomould in Fife, from development, updates, early evolution, and manufacture.
To test a plastic part, you have to take it beyond its ‘plastic limit’ – beyond the material’s elasticity, it should bend eventually, safely, if enough samples break, snap, or shatters, the whole batch fails. Either way, the samples/parts have to be taken past their limit. It gets recycled.
Polypropylene is a tough, resilient plastic, one of the lightest, and most resilient.
That is the material's attributes, shattering isn't. We caught the problem nine sales in.
These were recalled immediately, and replaced.
Comparison, production grade, and contaminated parts
One part plastic, one brittle, pure U77A eventually bends, beyond the limit, the new batch were snapping, even shattering
~ a few details of MANTA, and MantaB ~
designed in 2018, around the ischial area, optimising the design
upgrade in details for 2019, any rotation was resolved
2018 Soft-Grip™ updated for 2019
silicone is ideal, tough, resilient, designed for purpose
Soft-Grip™ above, on black-bronze element
grey Neoprene below, on pitch-black element
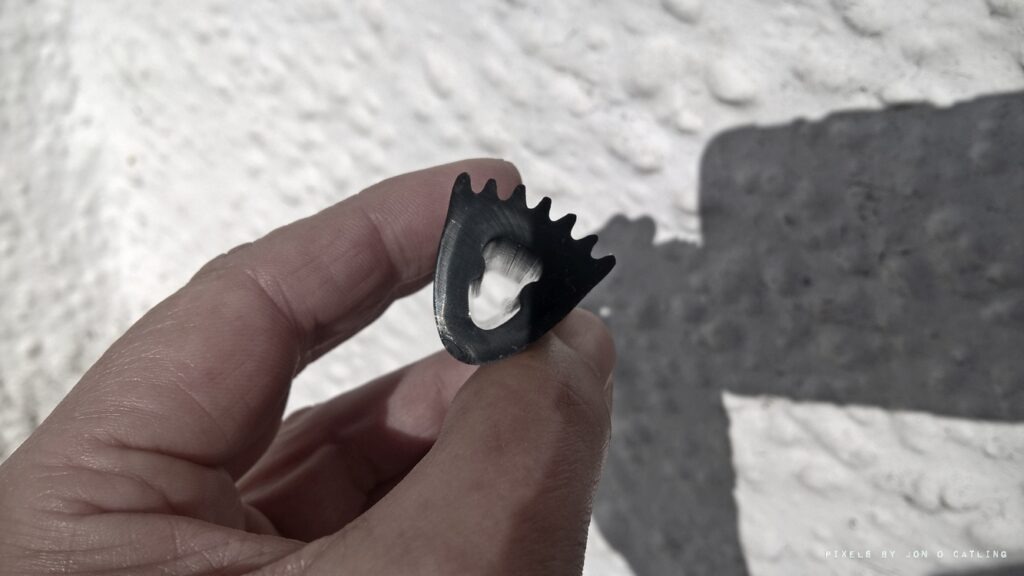
Soft-Grip design update, so surface pressure grips onto the elements
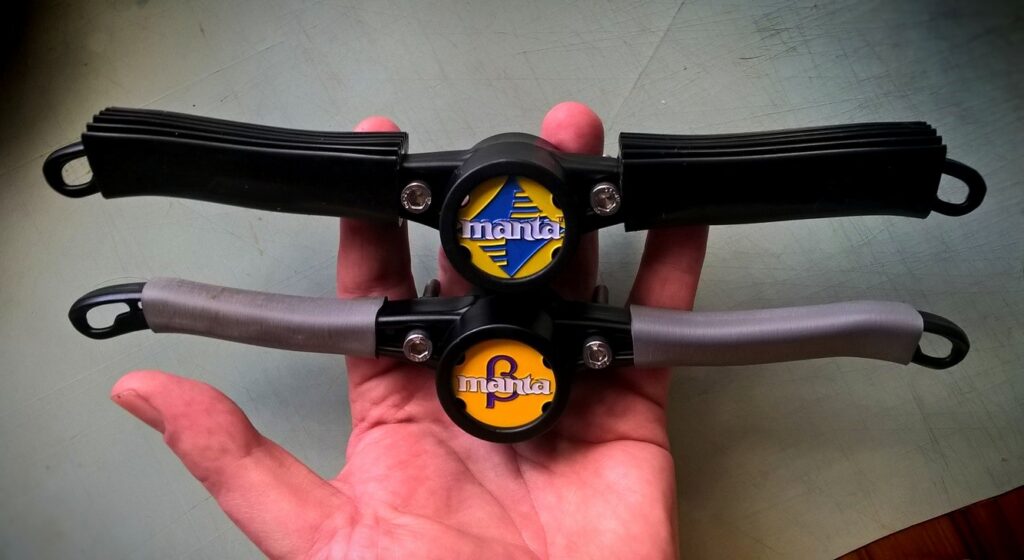
independent design, funding, development, manufacture